La demande mondiale portée par les terres rares "magnétiques" pour aimants permanents Nd-Fe-B
Au sein de la grande famille des terres rares (TR)1, quatre éléments chimiques aux propriétés magnétiques remarquables, à savoir : néodyme (Nd), praséodyme (Pr), dysprosium (Dy) et terbium (Tb), portent à eux seuls 90% de la valorisation du marché de ces métaux qualifiés de « mineurs », soit environ 1,7 milliards US$ par an (Roskill, 2019). Ces TR « magnétiques » sont utilisées sous forme d’alliages pour la production d’aimants permanents de haute performance, en particulier pour la technologie d’aimants néodyme-fer-bore (Nd-Fe-B)2. Les principaux moteurs de cette demande, progressant de près de 10 % par an, sont l’essor des véhicules électriques, de l'éolien off-shore, ainsi que celui de l’électronique et de la robotique, utilisant de grandes quantités d’aimants permanents.
La demande mondiale en aimants Nd-Fe-B étant de l’ordre de 125 000 t en 2019 est attendue à l’horizon 2030 selon les estimations entre 200 000 t (Roskill, 2020) voire jusqu’à 320 000 t dans les scénarios les plus optimistes (9,8 % de croissance annuelle moyenne).
En termes de volumes, la plus forte augmentation de la demande est attendue dans le secteur des véhicules électrifiés, passant de 9 % à 25 % du total en 2030 soit 50 000 t d’aimants Nd-Fe-B. L’électronique occuperait la deuxième place, avec 20 % du total, suivi du secteur éolien, avec une part qui pourrait atteindre 10 à 15 % en 2030, contre 9 % en 2019 selon Roskill.
L’impact le plus fort sur l’offre concerne l’augmentation de la production de Nd et Pr en particulier. Lors du processus de raffinage des TR, ces deux éléments sont séparés de manière concomitante du fait de leurs propriétés très voisines. L’oxyde Nd-Pr est l’intrant fondamental de la production des aimants permanents Nd-Fe-B. Or, pour une production actuelle de l’ordre de 45 000 t d’oxydes Nd-Pr à l’échelle mondiale, les capacités doivent doubler d’ici 2030 pour atteindre 90 000 t.
Les cas du dysprosium et du terbium sont légèrement différents, ces deux éléments étant ajoutés comme dopants dans les aimants Nd-Fe-B afin d’abaisser le point de Curie et d’autoriser un fonctionnement optimal à plus de 200°C. Ces conditions sont nécessaires en particulier dans l’éolien et l’automobile. Or, du fait de leur rareté et de leur prix, il existe de nombreuses tentatives pour limiter leurs usages ou les substituer de la part des utilisateurs. Leur production est de l’ordre 2 000 t par an, chiffre également amené à doubler d’ici à l’horizon 2030.
Pour ce faire, l’ouverture de nouvelles mines mais également de nouvelles capacités de séparation sont nécessaires. La Chine, qui représente déjà 60 % de la production minière mondiale de TR et 85 % de celle d’aimants permanents, l’a bien compris et continue de renforcer son positionnement sur ces marchés.
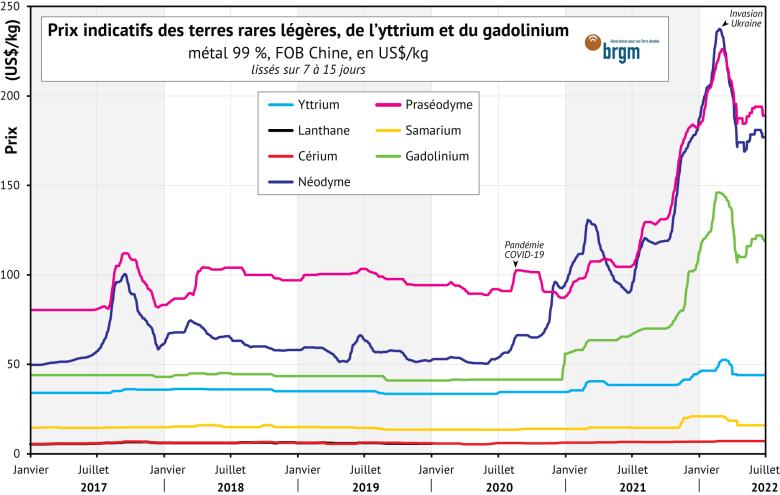
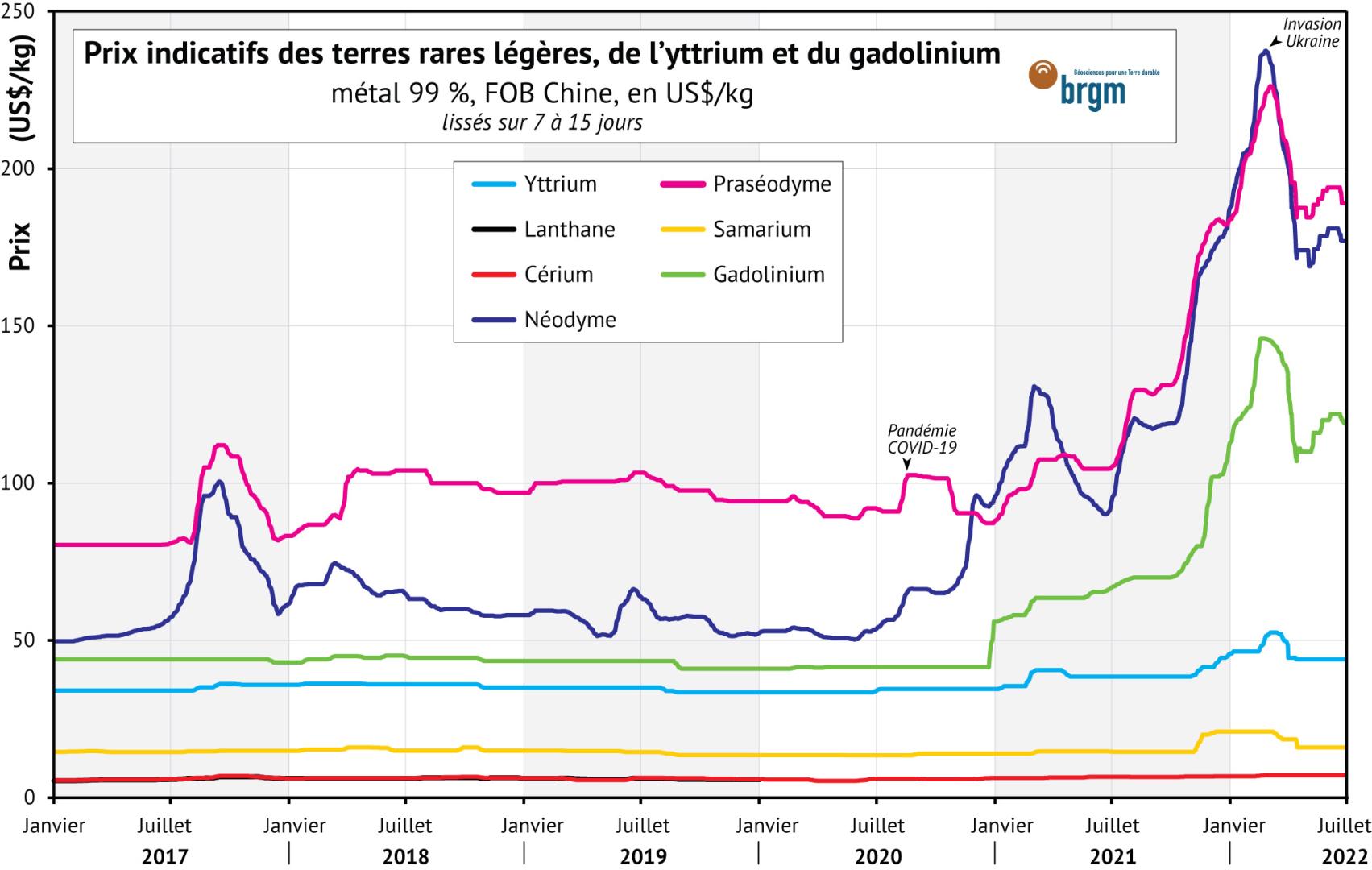
Prix indicatifs de l'yttrium, des terres rares légères et du gadolinium
© BRGM, d'après Argus Media lissés sur 7 à 15 jours
Renforcement des positions chinoises sur les chaînes de production, en particulier celles des aimants permanents
Le marché intérieur chinois dicte les prix internationaux des TR
Le premier signe de cette position dominante est le fait que les mouvements de prix des TR sont principalement régis par les événements du marché intérieur chinois. N’ayant pas de cotation sur les marchés boursiers, les prix des TR sont établis par négociation directe de contrats entre producteurs et transformateurs ou utilisateurs. Ces prix sont à considérer de manière individuelle par élément de TR, une grande disparité existant entre les terres rares légères, plutôt abondantes, et les terres rares lourdes réservées à des applications de niche du fait de leur rareté sur le marché. Ainsi, les prix du lanthane (La) et du cérium (Ce) s’établissent aux alentours 5 US $/kg, tandis que les plus chères, dont le terbium, peuvent dépasser 1 000 US $/kg.
En 2020, les mouvements de prix ont été relativement limités malgré le développement de la pandémie mondiale de COVID-19, avec deux raisons principales. D’une part, d’importants stocks avaient été accumulés en Chine avant la crise sanitaire ; cette dernière a ainsi permis leur écoulement progressif. D’autre part, malgré les interruptions temporaires de 70 à 80 % des capacités de transformation de terres rares en janvier et février 2020 liées au confinement (en particulier dans les régions du Sud, des provinces du Jiangxi et du Guangdong, plus proches de la ville de Wuhan), la plupart des capacités de traitement des TR lourdes ne fonctionnaient déjà pas à pleine capacité, ou concernaient des sites illégaux ou obsolètes. Ce sont donc les surcapacités du pays qui ont limité l’impact de la crise sanitaire sur la filière, les approvisionnements et les prix mondiaux.
A l’inverse, au cours de l’année 2021, les prix des TR ont connu un fort mouvement haussier. Exprimés sous forme métal 99 % FOB Chine, les prix du La et du Ce ont augmenté de 10 % en 2021, s’établissant à 6,4 US $/kg en moyenne, tandis que les prix des TR utilisés dans les aimants permanents ont explosé. Le prix du Tb, la plus chère des terres rares, s’est établi à 1 709,5 US$/kg contre 660,8 US$/kg en 2020, soit une hausse de 158 %, tout comme le Dy (+ 55,7 %) à 527,1 US$/kg, tandis que le Pr et le Nd sont passés respectivement de 93,6 US$/kg à 122,9 US$/kg (+ 31,3 %) et de 61,3 US$/kg en 2020 à 120,9 US$/kg en 2021 (+ 97,2 %).
Ce phénomène s’explique tout d’abord par des niveaux de stocks faibles des producteurs d’aimants chinois face à la reprise de la demande mondiale post-COVID début 2021. D’autre part, elle a semblé être une réponse du marché à l’introduction par la Chine de plusieurs mesures réglementaires, en particulier la nouvelle norme chinoise d'efficacité énergétique pour les moteurs électriques (plan 2021-2023), dont la mise en œuvre entraînerait une demande supplémentaire d’aimants Nd-Fe-B pour ce seul secteur atteignant 20 000 t/an sur le marché intérieur chinois.
Si les prix des TR sont cotés en dollars américains, l’un des objectifs de Pékin serait à terme d’imposer le Yuan comme monnaie de référence. A cette fin, une bourse d’échange sur les TR a été mise en place à Baotou, en Mongolie Intérieure, en 2018. Bien que cette place d’échange soit aujourd’hui uniquement tournée vers le marché intérieur chinois, les volumes qui y sont négociés augmentent progressivement, étant passés de 670 t en 2018 à 3 387 t en 2019 (selon Argus Media) comprenant des oxydes, des métaux et des alliages de TR. La Mongolie Intérieure vise à promouvoir la mise à niveau de cette dernière, afin de renforcer l'influence de la région sur le marché mondial des TR.
La Chine continue la restructuration de son industrie d'extraction et de valorisation des TR autour de deux grands pôles au sud et au nord du pays
Concernant l’amont de la chaîne de valeur, l’événement marquant de l’année 2021 est la création fin décembre d’une nouvelle entreprise d’Etat chinoise, conglomérat géant issu de la fusion de trois des principales sociétés d’exploitation des TR du sud du pays, à savoir Aluminum Corporation of China (Chinalco), China Minmetals et China Southern Rare Earth Group. La nouvelle entité, nommée China Rare Earth Group, a pour principal actionnaire la Commission de contrôle et d'administration des biens de l'État du Conseil d'État, avec une participation de 31,2 %. Les trois sociétés citées précédemment détiennent chacune 20,3 %. Enfin, deux sociétés de recherche, China Iron & Steel Research Institute Group et Grinm Group Corp., détiennent chacune une participation de 3,9 %. Comme annoncé par le gouvernement chinois, la fusion vise à intégrer les ressources en amont, à augmenter le pouvoir de tarification de la Chine sur le marché mondial et à utiliser les TR à l'avantage stratégique du pays. La nouvelle entité serait ainsi en mesure de produire environ 45 000 t d'oxydes de terres rares (OTR) par an, plaçant l’acteur China Rare Earth Group comme deuxième producteur de terres rares du pays après China Northern Rare Earth Group, exploitant le gisement de Bayan Obo. Ce dernier a également annoncé une restructuration début juin 2022, par la fusion de deux de ces entités : Baotou Huaxing Rare Earths, producteur d’alliages magnétiques de TR et Baotou Keri Rare Earth Materials, orienté vers des produits transformés à haute valeur ajoutée à base de TR.
En Mongolie Intérieure, au-delà de compter le premier site mondial de production et transformation de TR légères au monde (mine de Bayan Obo et complexe métallurgique de Baotou), la région autonome du nord du pays héberge aussi le principal centre de recherche au monde sur les innovations à base de terres rares, dans une zone industrielle colossale désormais appelée la « Baotou Rare Earth High-tech Zone ». Mise en place en 1992, cette zone dédiée aux TR vise à promouvoir les synergies entre l’industrie et la recherche pour accélérer le développement de la filière. Elle regroupe 9 000 entreprises et 73 centres de R&D, concentrant 3 300 brevets sur toute la chaîne de valeur, de l’extraction du minerai à la production d’aimants permanents et divers matériaux à base de TR. La zone de développement accueille notamment le Baotou Research Institute of Rare Earth (BRIRE), la plus grande institution de R&D chinoise dédiée aux TR.
Si la production d’aimants est principalement concentrée dans 3 autres provinces à savoir celles de Zhejiang (ville de Ningbo), de Shanxi et Pékin, la zone de Baotou domine l’étape de production des poudres magnétiques et alliages de haute performance utilisés pour construire les aimants Nd-Fe-B ou Sm-Co. Ayant aujourd’hui une capacité annuelle de production de 45 000 à 50 000 t de poudres magnétiques pour aimants permanents, l’ambition de la région autonome de Mongolie Intérieure est de doubler ce chiffre, pour atteindre une capacité de 100 000 t/an à l’horizon 2025, comme rappelé lors du forum annuel tenu en octobre 2020 (d’après Shanghai Metals Markets).
En outre, le 14ème plan quinquennal économique de la région (2021-2025) vise à « accélérer le développement de matériaux et d’alliages fonctionnels de terres rares de haute pureté, ainsi que celui de matériaux magnétiques de TR utilisés dans les machines-outils à commande numérique haut de gamme (Computer Numerical Control ou CNC). L'innovation technologique pour accroître les découvertes dans d’autres domaines sera également encouragée, notamment le développement d’un nouvel alliage de stockage d'hydrogène à base de terres rares, mais aussi l'amélioration des catalyseurs à base de TR dans les industries de l'acier, du ciment, de la verrerie, de l'automobile, de l'énergie thermique et de la pétrochimie ».
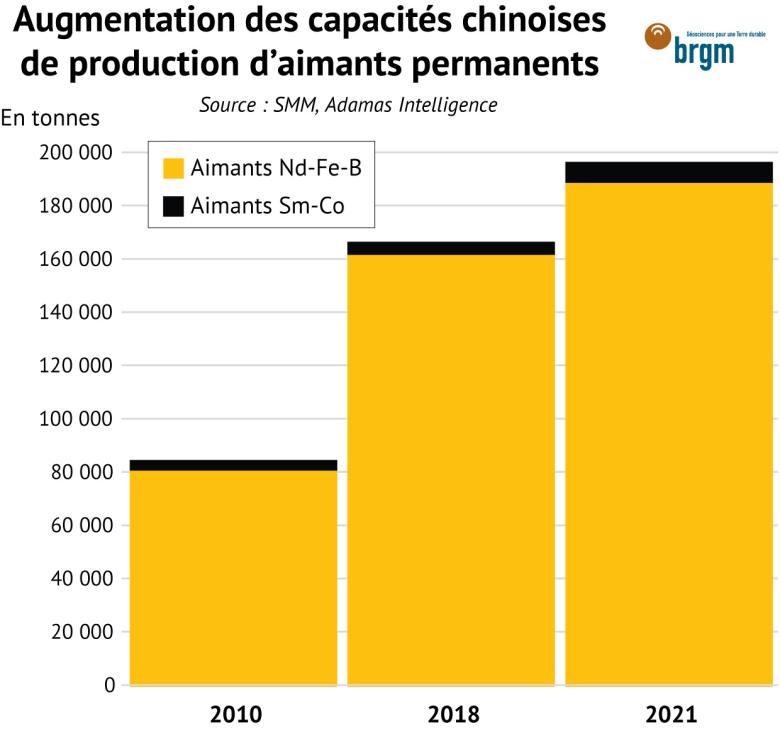
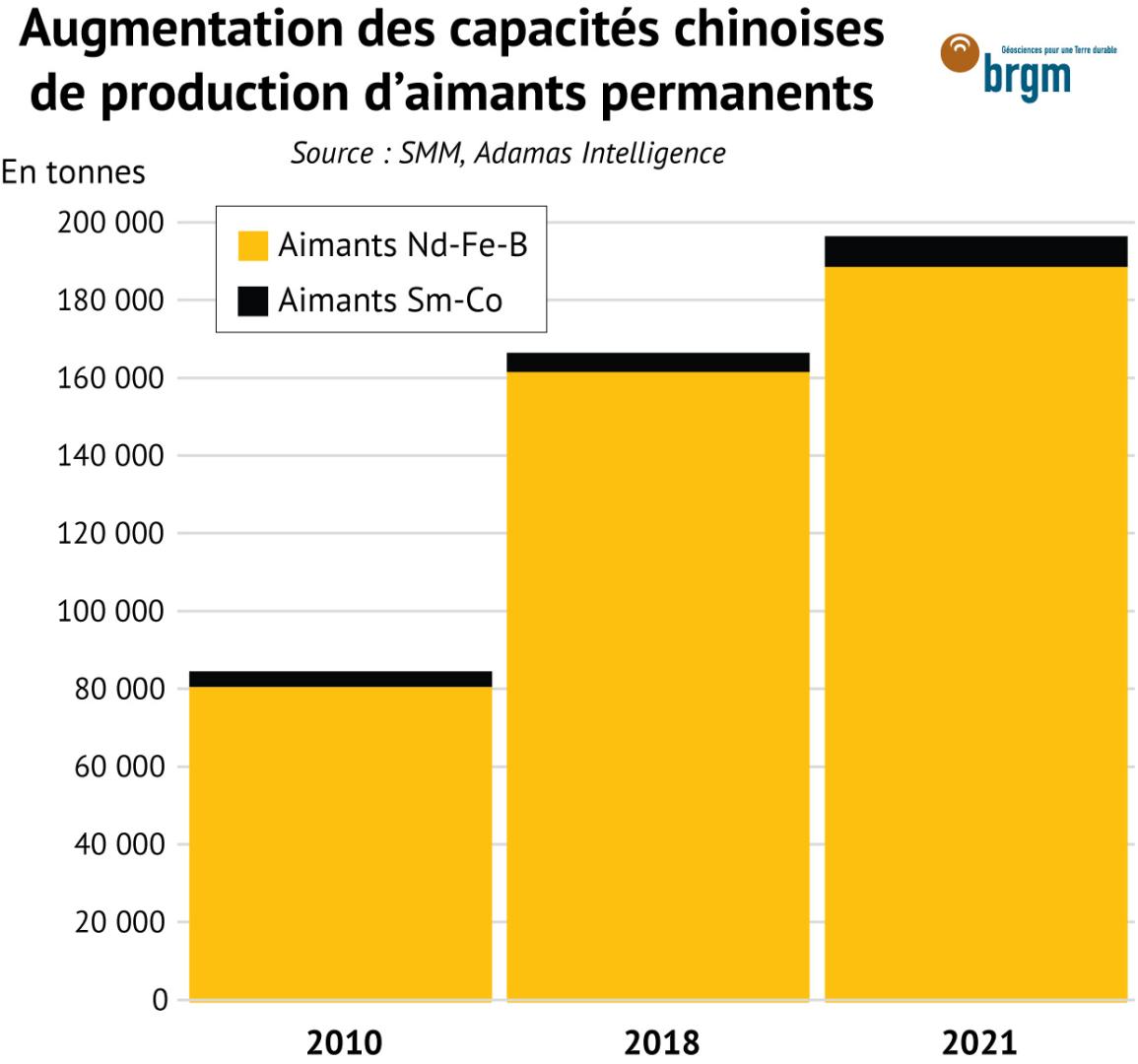
Augmentation des capacités chinoises de production d'aimants permanents entre 2010 et 2021
© BRGM, d'après SMM, Adamas Intelligence
La progression des capacités chinoises de production de production d’aimants permanents (Nd-Fe-B et Sm-Co) est fulgurante avec une production estimée à 195 000 t en 2021, contre 175 000 en 2019, 165 000 t en 2018, et seulement 83 000 t en 2010 (d’après les sources Argus Media, Adamas Intelligence). Cette industrie compte 3 principaux centres de production dans les provinces de Zhejiang (ville de Ningbo), de Shanxi et Pékin. La ville de Ningbo concentrait 40 % de la production totale de matériaux magnétiques à base de terres rares en 2019, avec 67 entreprises dédiées, dont l’entreprise Ningbo NingGang, premier fabricant de matériaux d'aimants permanents Sm-Co au monde, représentant 27 % de la production nationale et presque 20 % de la production mondiale. Par cette structuration, la Chine vise à être incontournable sur la réponse à la demande mondiale d'aimants permanents sur la période 2025-2030.
Enfin, la stratégie chinoise est visible sur deux autres secteurs d’influence en particulier :
- Les publications scientifiques de recherche académique et l’obtention de brevets sur les technologies innovantes de production et séparation des TR ;
- La standardisation
Dans le premier cas, une augmentation notable des publications scientifiques sur le sujet de la séparation des TR s’est confirmée durant la dernière décennie, la Chine étant passé de 30 publications internationales en 2011 à 140 en 2019, sur 360 publications sur ce domaine dans le monde (d’après Scopus). La Chine est également le pays recensant le plus grand nombre de dépôts de brevets sur ces étapes, la plupart provenant de la zone technologique de Baotou et des provinces du Sud. Elles s’inscrivent dans les « Plans de Développement » pluriannuels de la filière et tendent à répondre notamment aux problématiques de réduction de la pollution, paramètre très sensible de l’ exploitation des TR.
Dès 2011, des normes environnementales concernant les seuils tolérés de rejets dans les eaux usées et l’atmosphère étaient publiées. Puis en 2014, le Ministère pour l’Industrie et les Technologies de l’Information (MIIT) publiait le « Plan pour la promotion de technologies de production de TR propres », fixant des objectifs de pénétration de nouvelles technologies dans l’industrie des TR. Dans ce cadre, plusieurs dépôts de brevets sur de telles technologies ont été déployées à l’échelle industrielle sur de nombreuses lignes pilotes. L’une des principales était la séparation des oxydes de terres rares sans saponification afin de réduire les rejets d’ammoniac, source d’importants de dégâts environnementaux. En 2015, une ligne pilote d’une capacité de production de 2 000 t d’OTR construite par Jiangsu Guosheng Rare Earth, a permis une avancée dans ce domaine, avec le traitement de minerais sans rejets d’azote ammoniacal et avec le piégeage de plus de 90 % des rejets gazeux. Cette dernière a été déclinée depuis à l’échelle industrielle.
Sur le deuxième sujet, un comité technique a été mis en place en 2015 par l’Organisation Internationale pour la Standardisation (ISO) à la demande de la Chine afin d’établir des standards internationaux pour la production de TR et leur recyclage. Or, le comité technique ISO/TC 298 est présidé par l’administration de standardisation chinoise (SAC). Depuis son instauration il a abouti à 7 normes ISO publiées, notamment sur le recyclage. Par ce moyen, la Chine bénéficie de l’avance prise dans ces domaines pour imposer des références internationales. Le comité compte à ce jour 14 membres participants, dont la France, et 21 membres observateurs3.
Nouveaux acteurs et structurations de "chaînons manquants" dans le reste du monde
Face à ce constat, un certain nombre de pays tente de valoriser la montée en puissance de filières de production de TR pour réduire les risques de dépendance aux importations chinoises.
La figure suivante résume la chaine de valeur de la mine à la production des aimants permanents Nd-Fe-B.
Afin de remonter vers l’aval de la chaîne de valeur, l’une des étapes cruciales au-delà de l’ouverture d’une mine de TR est celle de la valorisation métallurgique. Deux types d’usines se suivent dans le processus : les premières sont des usines de traitement visant à purifier les concentrés de TR (extraire les éléments radioactifs et augmenter la concentration en TR valorisables), les secondes ont un degré de complexité supérieur : il s’agit de raffiner le concentré pour séparer des oxydes de TR purs (technologies d’extraction par solvant). Or la complexité de séparation dépend d’un minerai à l’autre et fait également varier le nombre d’étapes. Par exemple, à l’heure actuelle, l’entreprise australienne Lynas qui est la principale entreprise occidentale à maîtriser l’étape de séparation s’arrête à la séparation des TR légères pour produire un oxyde de néodyme-praséodyme (Nd-Pr). Cette étape aboutit à un concentré de terres rares lourdes mélangées (appelé SEG pour samarium-europium-gadolinium) qui est vendu en Chine, seul pays disposant d’installations de séparation de ces TR lourdes à ce jour.
Trois étapes suivent la production d’oxydes Nd-Pr :
- La réduction à l’état métallique (potentiellement sous forme d’alliages – permettant l’intégration du fer et du bore)
- La production d’alliages ou de poudres magnétiques (précurseurs d’aimants permanents)
- La synthèse des aimants en elle-même
La carte suivante présente le panorama des acteurs mondiaux à chacune des étapes : mines en activité et projets miniers les plus avancés, complexes métallurgiques existants et en projets, mais également le recensement des capacités mondiales de recyclage (ciblé uniquement sur celui des aimants permanents Nd-Fe-B, présentant les plus forts enjeux).
Production minière
Concernant la production minière mondiale de TR, elle peut être estimée en 2021 de l’ordre de 280 000 t à 300 000 t OTR (diverses sources).
La Chine demeure le premier producteur mondial à hauteur de 60 %. La production chinoise officielle, régulée par des « quotas de production » par région et par producteur a augmenté de 20 %, s’élevant à 168 000 t d’OTR contre 140 000 t en 2020. Pour la plupart des analystes, cette augmentation des quotas était quasiment inévitable étant donnée la situation actuelle de l'offre en Chine et la croissance de la demande des fabricants d’aimants Nd-Fe-B.
Les Etats-Unis sont aujourd’hui le deuxième producteur mondial en termes d’opérations minières, avec la reprise de la mine de Mountain Pass en Californie par l’opérateur MP Materials. En 2021, 43 000 t d’OTR ont été extraites selon l’US Geological Survey, destinées à produire des concentrés de TR, exportés et revendus par le partenaire chinois Shenghe. Des extensions de capacités sont prévues à partir de 2023, afin d’aboutir à la production d’oxydes Nd-Pr et de précurseurs d’aimants permanents sur le sol américain.
Avec sa mine de Mount Weld, la société australienne Lynas est la principale entreprise occidentale de production et de raffinage de TR. L’étape de séparation des TR légères est maitrisée et effectuée au sein de l’usine malaisienne de Gebeng. Pour l’année 2021, 15 600 t d’OTR séparées ont été produites dont 5 400 t d’oxydes Nd-Pr à haute valeur ajoutée. Cette production est estimée alimenter 65% de la fabrication des aimants permanents Nd-Fe-B au Japon, du fait de relations étroites mises en place avec les industriels du secteur dès les années 2010. Le reste de la production de Lynas se compose d’oxydes de cérium et de lanthane (~8 000 t) de moindre valeur et destinés pour la plupart aux marché de la catalyse, et enfin d’un concentré de terres rares lourdes mélangées appelé SEG pour samarium-europium-gadolinium (~2 000 t) vendu en Chine pour séparation. La compagnie a plusieurs projets d’extension : en Australie tout d’abord avec la construction d’une usine de purification (extraction des éléments radioactifs) à Kalgoorlie, qui sera opérationnelle en 2023. Aux Etats-Unis, Lynas a reçu un financement du Pentagone pour la construction d’une usine de séparation des terres rares légères au Texas : 5 000 t/an dont 1 250 t d’oxydes Nd-Pr. A cela s’ajoute une promesse d’investissement de 30,4 millions US$ pour travailler sur la faisabilité économique de la séparation de terres rares lourdes aux Etats-Unis.
Dans le reste du monde, des productions modestes peuvent être mentionnées, notamment en Russie dans la péninsule de Kola où la société Solikamsk affiche une production de 2 700 t d’OTR sous forme de concentrés de TR. De la même manière, des concentrés de TR sont produits au Burundi à Gakara (Rainbow Rare Earths), au Brésil à Araxá (CBMM) en sous-produit du niobium, en Inde dans les provinces de Kerala et Tamil Nadu (Indian Rare Earths Ltd.) ou encore en Thaïlande (province de Phuket), au Viet Nam (Yen Phu) ou au Myanmar (province de Kachin), ce dernier pays ayant émergé comme une source notable de TR lourdes à partir de 2018, l’essentiel étant importé par la Chine.
Complexes métallurgiques de traitement/séparation des TR légères
En 2021, près d’une dizaine d’usines métallurgiques était en construction à travers le monde. Ces projets sont concentrés en Australie, aux Etats-Unis, au Canada et en Europe.
L’Australie semble le prochain relais de croissance de la production occidentale de TR. Plusieurs projets miniers ayant déjà résisté à la crise de 2010 sont désormais proches d’une mise en production :
- L’entreprise Arafura Resources, avec le projet de Nolans Bore situé à 135 km au nord d’Alice Springs : la compagnie a reçu le soutien du gouvernement australien (30 millions A$) pour aider à la construction de l’usine de séparation dont la capacité de production est estimée à 7 000 tonnes/an d’oxyde Nd-Pr. La décision finale d’investissement est prévue au deuxième semestre 2022 ;
- L’entreprise Iluka Resources, historiquement productrice d’ilménite, zircon et rutile envisage deux opérations minières et une usine de séparation à Eneabba (Australie Occidentale) et Wimmera (Victoria). La construction de l’usine débutera en 2022 pour un début de production prévu en 2025. A terme, une capacité de 15 000 t/an de concentrés est envisagée (à partir de monazite et de xénotime). Le gouvernement australien soutient également le développement de l’usine de séparation, qui aurait pour finalité de pouvoir traiter des concentrés d’autres sources ;
- L’entreprise Australian Strategic Minerals, avec le projet Dubbo en Nouvelle-Galles du Sud. La particularité du projet (coût total estimé à 800 millions A$) est de ne pas dépendre uniquement des TR. En effet, 43 % des revenus proviendraient du zirconium devant les TR (30 %), assurant ainsi une moindre exposition aux risques de mouvements de prix ;
- L’entreprise Northern Minerals, avec le projet de Browns Range, qui s’étend de la mine à l’usine de séparation. La mise en production est attendue à l’horizon 2025.
Aux Etats-Unis, une nouvelle stratégie a émergé suivant les accords passés à l’été 2019 entre les gouvernements américains et australiens notamment, pour des collaborations renforcées sur le sujet des TR. En novembre 2020, le département américain de la Défense a accordé trois subventions liées aux TR d'une valeur de 13 millions US$ aux sociétés MP Materials, TDA Magnetics Inc et Urban Mining pour aider à la construction d’une ou plusieurs usines de séparation des TR.
Aux Etats-Unis toujours, la compagnie Energy Fuels a déclaré fin 2020 avoir produit des premiers concentrés de TR à partir de sables à monazite de Géorgie. Un accord a été conclu avec la société canadienne Neo Performance, opérant l'usine de séparation Silmet en Estonie pour la transformation ultérieure en matériaux avancés à base de TR. Energy Fuels envisage de traiter au moins 15 000 t de monazite par an.
Les compagnies USA Rare Earths LLC et Texas Mineral Resources Corp ont également officialisé l’ouverture d’une usine pilote dans le Colorado pour valider leur technologie de séparation des TR, pour un budget de 10 à 12 millions US$ et continuent le développement du gisement Round Top au Texas.
Au Canada, le gouvernement de la Saskatchewan a annoncé en juillet 2021 un financement de 31 millions C$ pour une installation de traitement de TR à Saskatoon qui appartiendra et sera exploitée par le Saskatchewan Research Council («SRC») et la société Search Minerals. L'usine aura la capacité de traiter des concentrés de TR pour les séparer en utilisant un procédé d'extraction par solvant.
En Russie, le gisement de Tomtor s’approche progressivement d’une mise en production. Un atout supplémentaire est la prise d’intérêts du groupe minier russe Polymetal en mars 2020, producteur d’or et d’argent dont la capitalisation boursière est estimée à 6 milliards US$. Celle-ci s’élève à 9,1 % du projet. Les ressources du projet étaient évaluées en 2018 à 30,5 Mt de minerai avec des teneurs de 10,6 % OTR et 4 % Nb. Les opérations comprendront une mine à ciel ouvert avec une usine de traitement (coût total estimé à 259 millions US$). La position stratégique de cette usine, à proximité de la ville de Krasnokamensk, près de la frontière de la Russie avec la Chine en fait un projet particulièrement important, d’autant plus dans un contexte de tensions géopolitiques accrues.
En Suède, le projet Norra Kärr, en phase d’exploration, mis à l’arrêt entre 2017 et 2020 pour des raisons environnementales a obtenu une extension du permis d’exploration jusqu’en août 2025. Une étude de faisabilité a été menée au cours de l’été 2021 par le nouvel exploitant (Leading Edge Materials) afin de revoir le modèle d’exploitation et convaincre de la viabilité de l’exploitation minière.
Un autre projet est porté par l’entreprise LKAB en Suède, exploitant de la mine de fer de Kiruna et dont l’objectif est de prouver la faisabilité de traiter les TR contenues dans les résidus miniers (apatite) afin d’obtenir 10 à 15 000 t/an de concentrés de TR. De la même manière, l’entreprise Yara, en Norvège, étudie la possibilité de récupérer des TR à partir de l’exploitation d’engrais phosphatés.
En Grande Bretagne, l’entreprise Pensana Rare Earths développant un projet minier à Longonjo en Angola s’est engagée à construire une usine de purification des TR sur le territoire britannique. Cet objectif est similaire pour l’entreprise britannique Rainbow Rare Earths, produisant au Burundi des concentrés de TR et ayant annoncé relever ses objectifs à 6 000 t de concentrés/an, avec une purification en Grande Bretagne.
Enfin, en Pologne, le groupe Azoty Pulawy, acteur majeur des produits chimiques, s’est associé en juillet 2021 à Talaxis Limited développant un projet minier au Malawi avec l’entreprise canadienne Mkango Resources pour la construction d’une installation de traitement des TR (purification et séparation) sur le sol polonais.
Au Groenland, le gisement de Kvanefjeld pourrait devenir le 2ème producteur mondial. Il s’agit d’un des plus gros gisements de TR au monde (10 Mt d’OTR contenus dans les ressources), avec une production de 32 000 t/an de concentrés envisagée d’après l’étude de faisabilité finalisée en 2019. Cependant, le nouveau gouvernement du Groenland a décrété un ban sur l’exploitation de minerais contenant plus de 100 ppm d’uranium début novembre 2021, rendant impossible l’exploitation du gisement sans changement ultérieur.
Usines de recyclage des aimants permanents Nd-Fe-B et positionnement français
A l’heure actuelle, le recyclage des aimants permanents Nd-Fe-B n’est effectué qu’en Chine et au Japon.
Toutefois, les deux modèles diffèrent :
- Au Japon les filières se sont structurées dès les années 2010, en ciblant la récupération en fin de vie des appareils commercialisés par les utilisateurs de terres rares eux-mêmes (équipements électroniques, compresseurs des climatiseurs, etc.). Les principaux acteurs sont Hitachi, Shin Etsu, Showa Denko, Mitsubishi Materials, Toyota Tsusho. En 2020, Hitachi estimait que les filières de recyclage mises en place par le groupe contribuaient à 10 % de leur approvisionnement en aimants permanents. Selon la même source, cela correspond à 26 t, exprimées en contenu de terres rares recyclées, depuis 2013 ;
- En Chine, les activités de recyclage semblent essentiellement se concentrer sur les chutes de production d’aimants permanents ou scraps, en particulier dans les provinces du Shandong et du Jiangxi (d’après Shanghai Metals Market)
Dans le reste du monde, les initiatives se multiplient les plus visibles étant nord-américaines et européennes :
- GéoMega au Canada
- Urban Mining Company aux Etats Unis
- Hypromag au Royaume-Uni
- Carester, MagREEsources, Orano et Arelec en France
Deux grandes possibilités existent pour recycler les aimants permanents :
- La boucle courte aussi schématisée par le terme « magnet to magnet »: les aimants usagés sont broyés pour obtenir une poudre d’alliage magnétique, qui peut être réutilisée pour fabriquer de nouveaux aimants permanents, avec de potentielles pertes de performance ;
- La boucle longue : les aimants sont broyés, puis des traitements permettent d’obtenir des oxydes purs de TR. L’avantage est de ne pas dépendre de la qualité et de permettre de s’adapter aux évolutions technologiques, notamment en cas d’évolution des proportions des différents composants des alliages magnétiques. Toutefois, cette voie est dépendante des capacités industrielles à produire des aimants permanents à partir des oxydes.
Le schéma ci-contre présente les principaux projets en phase de pré-industrialisation et leur positionnement entre les modèles de boucles courte et longue. Comme l’illustre le cas français, ces deux modèles ne s’opposent pas, n’ayant pas les mêmes sources ni les mêmes débouchés. Ils pourraient donc s’intégrer de manière complémentaire.
Enjeux de mise en place d'une filière de recyclage des aimants permanents Nd-Fe-B en France
Une étude menée en 2021 par la Direction Générale des Entreprises (DGE) au sein du Ministère de l’Économie et des Finances a identifié 3 gisements les plus importants pourvoyeurs d’aimants permanents Nd-Fe-B à recycler sur le territoire national. Ce sont les véhicules électriques et hybrides, les éoliennes en mer (off-shore) et les déchets d’équipements électriques et électroniques ou D3E (exemples : trottinettes, condensateurs de réfrigérateurs, etc.).
Filière automobile - Véhicules hors d'usage (VHU) : des compétences spécifiques de démantèlement à créer
La filière qui semble la plus avancée et la plus pertinente sur cette problématique est celle des VHU, le gisement potentiel à l’horizon 2030 étant le plus important. Plusieurs verrous sont néanmoins à lever sur cette filière.
Premier constat : les équipements contenant les aimants permanents des VHU ne sont ciblés par aucune obligation réglementaire ni aucune incitation économique à ce jour. Actuellement, les centres VHU ont l’obligation de retirer uniquement : les batteries, les huiles usagées et les filtres, les liquides de refroidissement ou de freins et les fluides de climatisation.
Deuxième constat : l’enjeu principal concernant les principaux équipements contenant des aimants Nd-Fe-B dans les VHU est le démontage, nécessitant du personnel formé que tous les centres de VHU ne possèdent pas.
La première étape serait donc que des consignes des constructeurs automobiles soient données aux centres de VHU mais également aux centres de broyage, par le biais de la plateforme automobile (PFA), afin de cibler le démontage des principaux équipements contenant des aimants Nd-Fe-B dans les véhicules : les axes de direction, les haut-parleurs ou les lève-vitres et les moteurs dans le cas des véhicules hybrides et tout-électriques. Les premières cibles seraient les centres VHU agréés qui traitent plus de 1 000 VHU par an et qui appartiennent à au moins un réseau de constructeurs automobiles. Ces centres pourraient être plus facilement sensibilisés à l’intérêt du retrait des aimants permanents Nd-Fe-B en bénéficiant d’une animation des constructeurs. L’étude de la DGE fait ainsi apparaître que 277 centres VHU seraient concernés comme étant les plus à même d’extraire les aimants permanents des véhicules en fin de vie, représentant 44 % du nombre total de VHU traités en 2018 d’après l’ADEME. Un critère supplémentaire pourra être de privilégier les centres ayant déjà une compétence dans le démontage de pièces. Ce nombre est plus élevé car 61 % des centres VHU sont des démonteurs de pièces de réutilisation et traitent 69 % du nombre total de VHU. Toutefois, les compétences spécifiques nécessaires au démontage des équipements contenant les aimants seraient à vérifier.
L’étape suivante est également de sensibiliser les centres de broyage. En effet, à ce jour, ces derniers récupèrent les différentes pièces qui ne sont pas démontées dans les centres de VHU, dont celles contenant des aimants. Ces centres broient directement les carcasses des VHU, puis récupèrent certains métaux et autres matériaux facilement revendables. A ce jour, les aimants permanents ne peuvent pas être récupérés par ce biais car les centres de broyage ne sont pas équipés d’appareils permettant leur extraction. Les aimants sont donc soit endommagés lors de la phase de broyage ou bien mélangés à d’autres matières. Il existe actuellement 47 centres de broyage sur le territoire français, dont 27 sites dépendant uniquement de 3 groupes industriels (Derichebourg, Galoo et Ecore). Ces acteurs traitent 70 % du flux de carcasses de VHU traités en France, ce qui représente donc un levier d’action intéressant.
Deux conclusions découlent : la première est la nécessité de former un personnel compétent dans le démontage manuel ou semi-automatisé de pièces contenant les aimants. Cela représente une opportunité de formation et de création d’emplois potentiellement importante.
La deuxième est celle de l’équation économique. Il faut en effet qu’un nouveau modèle axé sur le recyclage soit plus rentable que la revente des métaux issus des carcasses des VHU tel que pratiquée actuellement. Il faut donc évaluer et s’assurer que le coût du démontage, du stockage et de la collecte pour la revente des aimants permanents en fin de vie soit rentable pour les centres de VHU et les broyeurs. Une étude financée par l’ADEME doit permettre d’analyser la faisabilité d’un tel démontage, l’accessibilité de ces pièces et son coût.
Filière de l'éolien
Pour l’éolien en mer, le démantèlement est compliqué et il convient de concevoir le démontage des aimants permanents dès la conception. La logistique pour le démontage est lourde, car cette opération se situe en mer avec d’importants moyens logistiques de transport, de levage et de démagnétisation. Le circuit de collecte de ces éoliennes off-shore est donc entièrement à construire. Les premières éoliennes à attaque directe et avec aimants permanents ont été installées en 2015 par Siemens Gamesa sur le parc de Westermost Rough (35 éoliennes de 6 MW) et seront à recycler potentiellement après 20 à 30 ans d’utilisation, soit au plus tôt vers 2035/2040.
Filière D3E
Bien qu’ils soient un important gisement dans le secteur des D3E, les disques durs d’unités centrales d’ordinateurs ne représente que 3 tonnes par an, soit environ 1 tonne d’aimants permanents et environ 330 kg de Terres Rares par an, ce qui parait faible en terme de potentiel valorisable à court terme.
Des questions fondamentales sont à résoudre concernant la mise en place des phases de collecte et de démontage efficaces, n’augmentant pas considérablement le coût de ces filières de recyclage. Le projet de recherche européen Valomag, piloté par Suez et réunissant notamment le BRGM et le CEA, a pour ambition d’y apporter des réponses.
Acteurs français
Quatre projets de pilotes industriels sur le territoire français visent actuellement le recyclage d’aimants permanents à TR :
- Celui porté par la société Carester. Un démonstrateur industriel appelé CAREMAG sera implanté à Lacq à l’horizon 2024. Fondé sur le modèle de la boucle longue, l’objectif est de traiter 1 000 t d’aimants Nd-Fe-B en fin de vie par an, de tous types, pour produire des oxydes de TR purs. A terme, le principal marché ciblé est celui de l’automobile.
- Celui porté par la société MagREEsources, reposant sur la boucle courte. Une ligne de production pilote prévue pour septembre 2022 attaquera dans un premier temps le marché des plasto-aimants. A plus long terme, l’objectif est la re-fabrication d’aimants frittés de haute performance reposant sur des sources d’aimants en fin de vie bien identifiées et de compositions connues et stables, comme par exemple, les aimants des éoliennes en mer ;
- Le projet MAGNOLIA, piloté par Orano à Châtillon (92), implique quatre autres partenaires (CEA, PAPREC, DAIMANTEL et VALEO). Il a pour ambition de structurer un outil industriel de fabrication d’aimants permanents haute-performance.
- Celui de la start-up REEfine technologies, implantée à Lyon, travaillant avec l’entreprise ARELEC qui compte développer un atelier pilote de production de poudres coercitives anisotropes à Grenoble. En février 2022, elle s’est associée aux entreprises Celimer, Poral et ECM Technologies pour mener à bien son projet visant les contenants cosmétiques, la domotique et les petits moteurs électriques. Les premiers aimants recyclés sont attendus courant 2023.
Conclusions
Une plateforme semi-industrielle existe depuis 2016 en France dédiée à la recherche technologique sur les aimants permanents, exploitée par le CEA Liten. La capacité de la ligne pourrait être portée en 18 mois à une production annuelle de 4,5 t d’aimants. Dans cette configuration, la plateforme pourrait constituer le point de départ pour recréer une filière de fabrication d’aimants complète à l’échelle nationale ou européenne, sur laquelle toute filière de recyclage devra s’appuyer pour se développer.
Encore à ce jour, les principaux enjeux pour la reconquête d’une souveraineté industrielle dans la production de terres rares ou d’aimants permanents sont économiques, les utilisateurs finaux étant contraints de comparer le prix final d’un aimant permanent recyclé avec le prix d’un aimant permanent chinois primaire, à performances égales.
Notes :
1 : Comprenant les 15 lanthanides et l'yttrium. Pour la définition complète, voir le document.
2 : Les aimants samarium-cobalt (Sm-Co) sont une autre technologie d'aimants permanents à base de terres rares. Développés à partir des années 1970, ils ont perdu des parts de marché aux dépens des aimants Nd-Fe-B du fait de leur prix élevé. Leur part de marché est toutefois stable et ils demeurent privilégiés dans certaines applications où leur petite taille et leur plus grande stabilité aux hautes températures (jusqu'à 550°C) sont indispensables.
3 : Informations à retrouver sur le site de l'ISO.
Auteur : Gaétan Lefebvre, BRGM
Illustrations : Nicolas Charles et Johann Tuduri, BRGM
Références :
Adamas Intelligence https://www.adamasintel.com/
Argus Media https://www.argusmedia.com/en
Roskill https://www.woodmac.com/nslp/roskill/landing-page/
Shanghai Metals Market https://www.metal.com/
Scopus https://www.elsevier.com/fr-fr/solutions/scopus